Success Story: ultimate Training Munitions
ruf Aluminum briquetting squeezes more profit into ultimate training munitions’ pocket
Integrate Seamlessly. Purge Unwanted Waste. Create New Revenue.
CLIENT
Ultimate Training Munitions (UTM) is headquartered in the United Kingdom, UTM also has production facilities in the United States and a global sales network operating in 45 countries.
EXECUTIVE SUMMARY
UTM makes high-performance training ammunition and safety systems that allow armed forces and law enforcement agencies in the U.S. and around the world to conduct safe and effective Close Quarter Battle (CQB) training exercises.
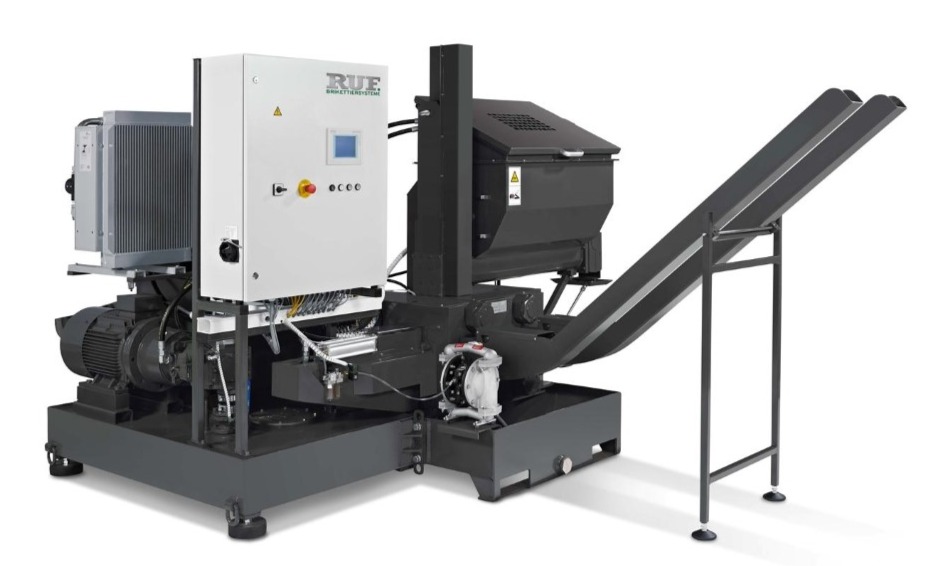
CHALLENGE
UTM’s U.S. factory housed 10 machines in 60,000 square feet of space. During their high-speed aluminum turning process, precision munitions and system components are turned and finished.
UTM was forced to dispose of oily turnings – primarily in hoppers for draining before they were sold for next to nothing to scrap processors.
“Our moisture content threshold for getting optimum return for our chips is 2%. With RUF briquettes, our chips contain only 1.1% to 1.8% moisture. This drastically improves our chip resale revenues—by about 50 cents per pound.“
Ralf Wagner, Technical Director at UTM
Aluminum Briquetting SOLUTION
RUF Briquetting and UTM met at an international manufacturing technology trade show. After a production facility tour in Germany and breakdown of RUF’s innovative briquetting technology and systems, UTM was sold, and began working with RUF’s aluminum briquetting systems.
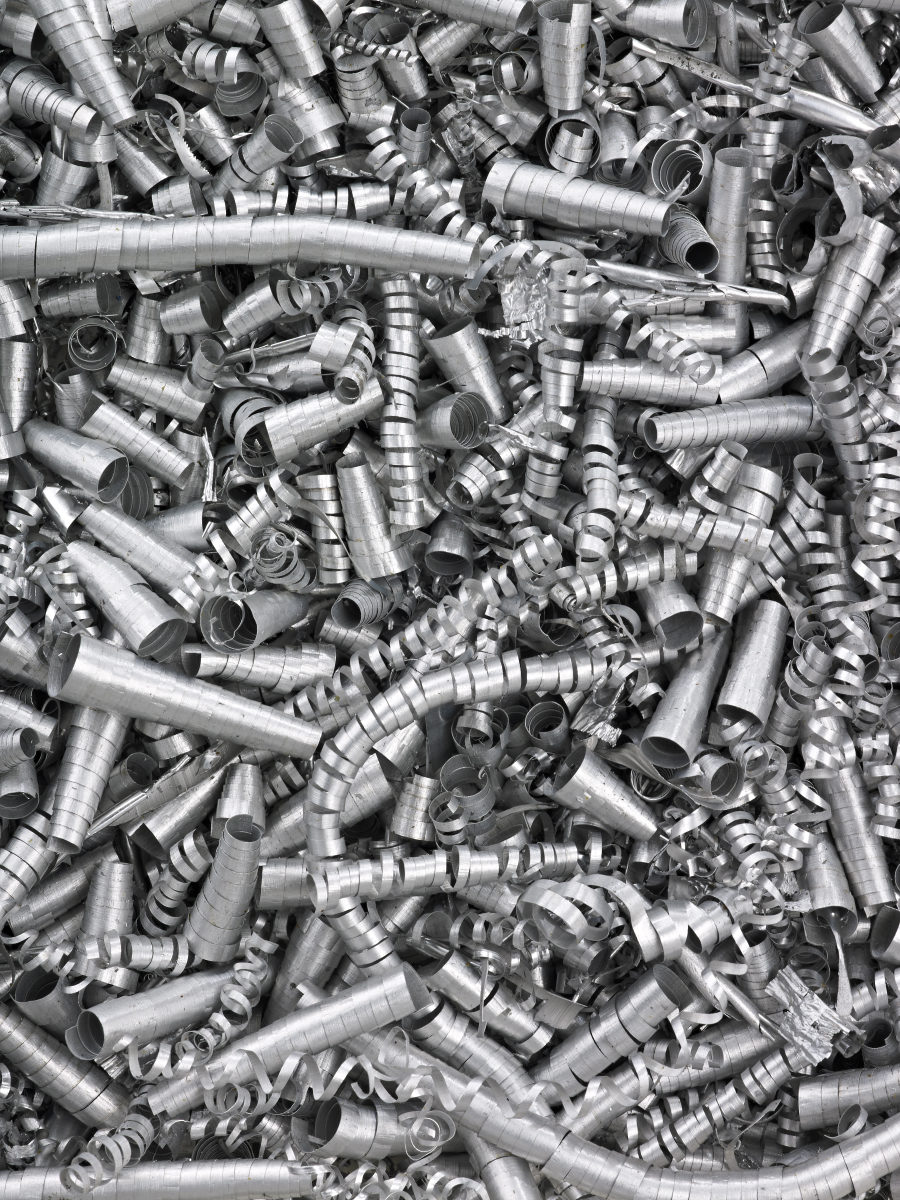
results
UTM is able to filter and reuse the processing oil it reclaims during the aluminum briquetting process.
UTM repeatedly recommends RUF and its
briquetting technology to other companies.
“RUF was a pleasure to work with every step of the way and were willing to do whatever it took to find the best solution.” Ralf Wagner, Technical Director at UTM
- UTM’s scrap revenue has grown 250%
- Factory is also cleaner and safer for employees
- UTM’s RUF Aluminum Briquetter paid for itself in less than 6 months
- Operational efficiency has risen and the scrap process is more streamlined
- Drain hoppers were omitted and 20% of valuable floor space was reclaimed